The weather had totally changed that morning. An icy wind was coming from the North and big grey clouds gathered in the east. Yesterday I still had good hopes for today’s pilgrimage, the sun promised me all would go well. She lied to me … again.
There was no place for hesitation, I planned this journey for so long and there was no way back. All the equipment was already packed, only my clothes I had to change. So I started less enthusiastic as I hoped, but this little draw back wasn’t going to stop me. This was to important, bigger than live. Bigger than my life for sure.
After a few miles the wind and rain tempered all what was left of my enthusiasm. Only knowing that there would be a rewarding acquaintance with the grand master kept me going. Mile after mile I needed to remind me of this reward to keep me going. I lost every sense of time and progress when suddenly I noticed I had reached the sanctuary that I was looking for. At the entrance gigantic wooden sculptures made me feel welcome and a scent of incense worked relaxing and made me forget the pain I endured. It was almost like coming home.
Garcia-Deschacht
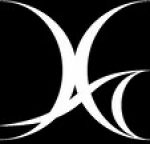
Contact@garcia-deschacht.com
Instagram: @garcia_deschacht
Facebook: Garcia Deschacht
Background on the maker(s)
Let me introduce you to Laura Garcia and Andy Deschacht. Together they think about the pen concepts, then Andy makes them and Laura makes the web page, pictures and videos. All is done with the support of the cuddling department.
Although Andy is a schooled cook, he always loved to create more permanent pieces of art. For years he made wooden sculptures and this passion is the one that he puts now by making the pens and pen boxes.
Materials and specialties
For the pens they often use vintage material. This can be old stock blanks from a.o. Omas and Conway Stewart or wood from Roman and medieval times, found on Belgian archeology sites. Nevertheless modern eye-catching materials like the McKenzie’s “DiamondCast” blanks are also beloved.
The metalworking on bands, clips and additional decoration is done in house. It is mostly done with copper, aluminum or bronze, depending on the design of the pen. The only ‘finished’ parts that are not handcrafted are the nibs, feed and housing. Peter Bock nibs are the chosen ones.
The laser engraving of the logo on the pens and sometimes on the wooden pen boxes is done external. The preparation of the wood is also done by Andy himself. All starts by choosing the best parts for the pens and the best parts for the pen boxes. Then the wood is sawn, dried in a small oven and stabilized in a homemade vacuum pot.
Turning to life
There are two major types of pen that are made. The first type is the ‘on command’ pen, where the client has a clear vision of the pen he/she wants.
And the second type is the ‘free’ pen. For this kind of pens Andy and Laura sit together in the evening and contemplate on what would be nice for the next creation. The feeling will determine the materials and form.
A rough lay-out of the pen is sketched and will lead Andy to start the next project. Because there are not ‘fix things’ when Andy gets into ‘the zone’ it happens by working that he shapes a pen based on his intuition.
All pens and pieces are turned individually using a metal and/or a rather small simple classic wooden lathe. This traditional approach gives Andy the chance to really feel what he is creating and that is the satisfaction he is looking for.
Garcia-Deschacht doesn’t work with standard models and they create a unique piece every time. Even when using the same material it will never be the same in length, width, general form or finish. Although making a more mass product batches of pens would speed up production and income, it is a path that Garcia-Deschacht doesn’t like to follow. It would be a burden for Andy because in that case he would lose his artistic freedom.
Production quantities and customers
The vision on manually creating unique pieces allows at the moment an average production of 2 to 4 pens every week. Most customers come via social media . Their pens are also present at the Scoopstores in Antwerp and Ghent.